イノベーションストーリーズ
機能材料
ディスプレイに不可欠の機能性フィルム
多様な人々の底力と逆転の発想で
危機を乗り越えてきた歴史
- 目次
ずっと不利だと思ってきたことが、ルールが変わると有利になることがあります。ただし、それにいち早く気づき、一歩踏み出すチャレンジができれば――。写真フィルムのベース(支持体)という目立たない材料から、液晶ディスプレイに無くてはならない素材となったTAC(タック)フィルムは、まさにそういう製品でした。
テレビをはじめ、ノートパソコンやスマートフォンなど、身近なデバイスのモニター画面としておなじみの液晶ディスプレイは、何層ものフィルムや偏光板、ガラスで液晶を挟んだ構造になっています。当社の機能材料事業の主力製品は、偏光板の保護フィルムであるプレーンなTACフィルムと、そこに光学的な機能を入れた視野角拡大用フィルムです。現在では複数の分野において、当社製品を通してお客様と深く繋がらせていただいておりますが、その歴史は事業存続の危機と成長機会との背中合わせの格闘の日々の連続でした。
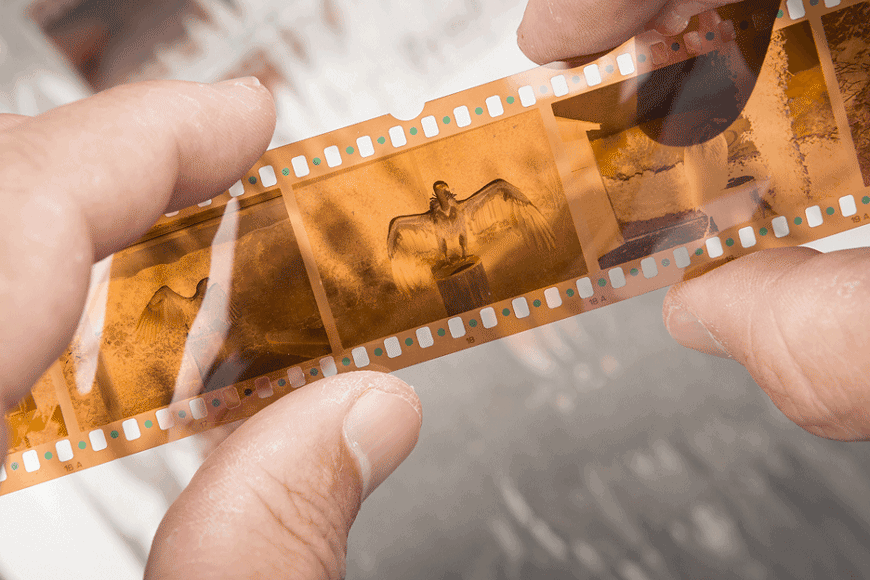
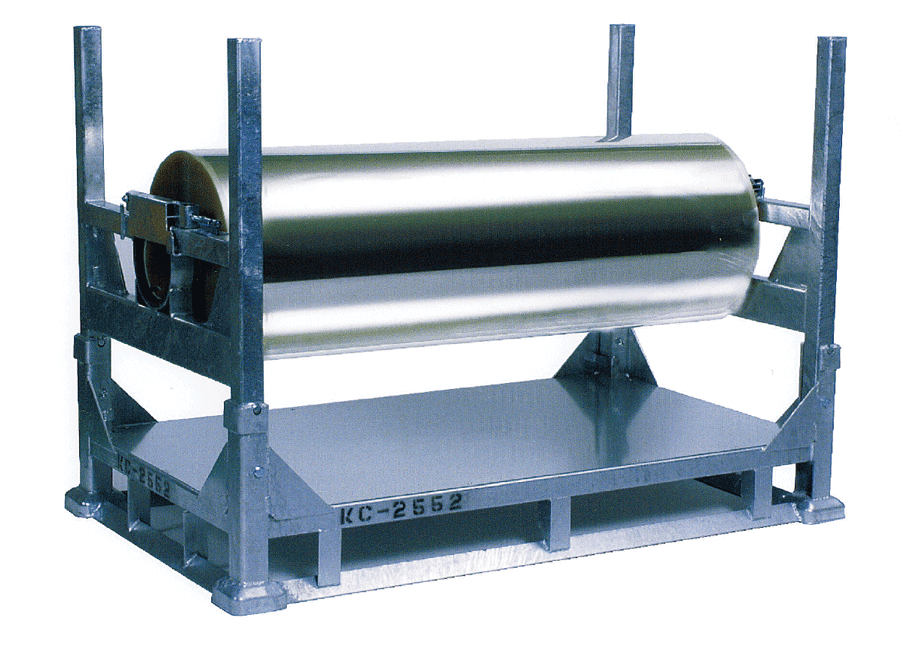
縁の下の力持ちからの挑戦
「TAC」とは、セルロースアセテートという樹脂の一種で、植物由来の物質を原料とし、環境への影響が小さく、紫外線に強く、高熱でも分解されず薬品にも腐食されにくいという特性があり、写真フィルムのベースとして燃えやすかったセルロイドに代わって1950年代から使われてきました。
最終製品の写真フィルムに仕上げるには、TACフィルムの上に乳剤と呼ばれる感光材料を10数層分一気に重ね塗りします。技術の壁が高いために参入は容易でなく、写真フィルムのメーカーは世界でも4社しかありませんでした。1990年代、写真事業は統合前のコニカの祖業でもあり主力事業でしたが、その技術における花形は乳剤塗布であり、TACフィルムの技術・生産は縁の下の力持ち的な存在でしかありませんでした。しかし彼らは「技術者としては引けを取らない」というプライドを胸に秘め、その品質や耐久性を徹底的に追求し続けていたのです。
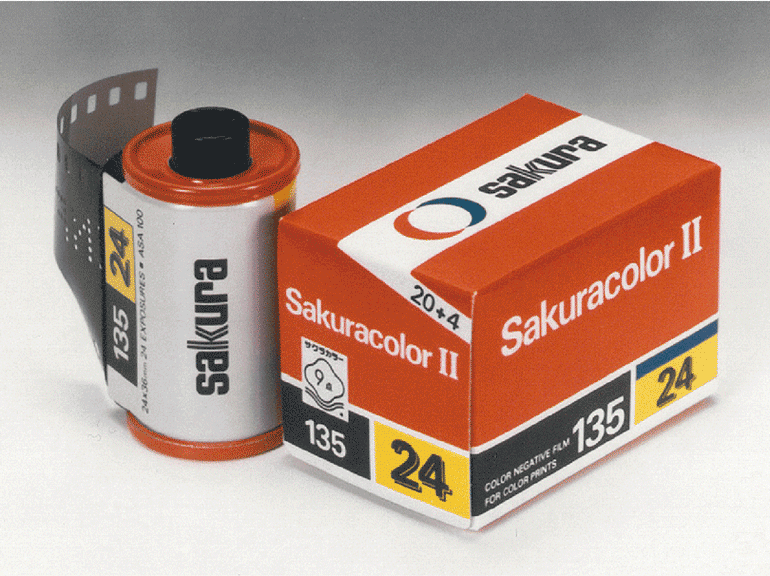
写真フィルムの需要は、カメラが一般家庭に浸透するにしたがってぐんぐん伸びていきましたが、1990年代半ばに大きな転機が訪れます。デジタルカメラの登場です。これから確実にカメラはアナログからデジタルに置き換わっていく。写真撮影にフィルムが要らなくなれば、TACで積み上げてきた技術も終わってしまうのだろうか?
その時、TACフィルムの技術者たちが動きました。当時ブラウン管に代わって普及し始めた液晶ディスプレイ用の偏光板の保護フィルムとしてTACフィルムが使えるという話を聞きつけると、偏光板を扱うメーカーに現物を持ち込み、売り込みをかけたのです。
そのチャレンジは実を結び、当社のTACフィルムは液晶パネル向けの光学フィルムとして再出発することになります。求められる品質は写真フィルムのベースに比べ格段に上がります。工場の立ち上げに苦労しながらも、2000年には神戸事業場内の新ラインでの生産にこぎつけました。その時は、わずか6年後に当社の写真フィルム事業が終焉を迎えるとは、実感を持って捉えていた人は少なかったのです。
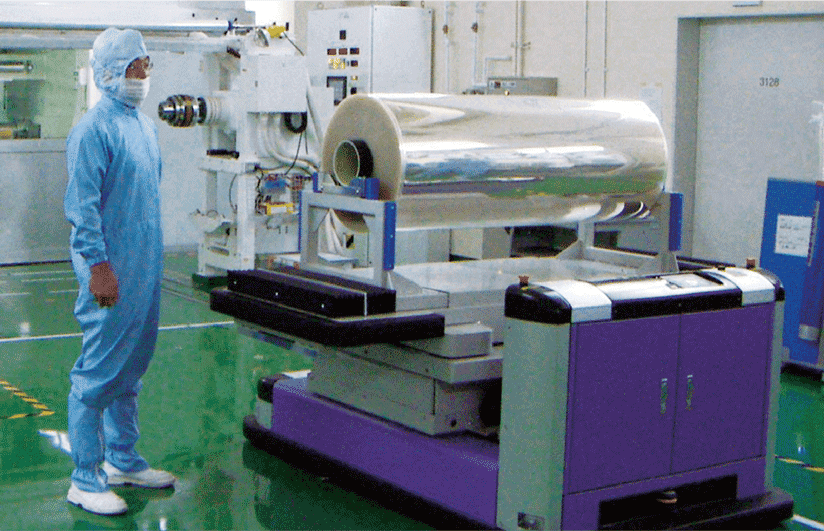
舞台が変われば不利が有利になる
新規事業として立ち上がったTACフィルムでしたが、出足は必ずしも順調ではありませんでした。安定した利益をなかなか確保できなかったのです。窮地に追い込まれながらも、技術者達はTACフィルムに光学フィルムとしての新しい価値を見いだそうと、2つの革新に挑みました。
1つ目は、薄膜化への挑戦です。写真フィルム用途では厚さ120ミクロン(0.12mm)だったものが、液晶ディスプレイの偏光板ではその3分の2の80ミクロン(0.08mm)が採用されていました。しかしそのころ台頭してきたノートパソコンでは製品の薄型化がトレンドとなっており、そこに使われる偏光板用TACフィルムでも更なる「薄さ」に商機があると考え、厚さ40ミクロン(0.04mm)という薄膜づくりに挑んだのです。
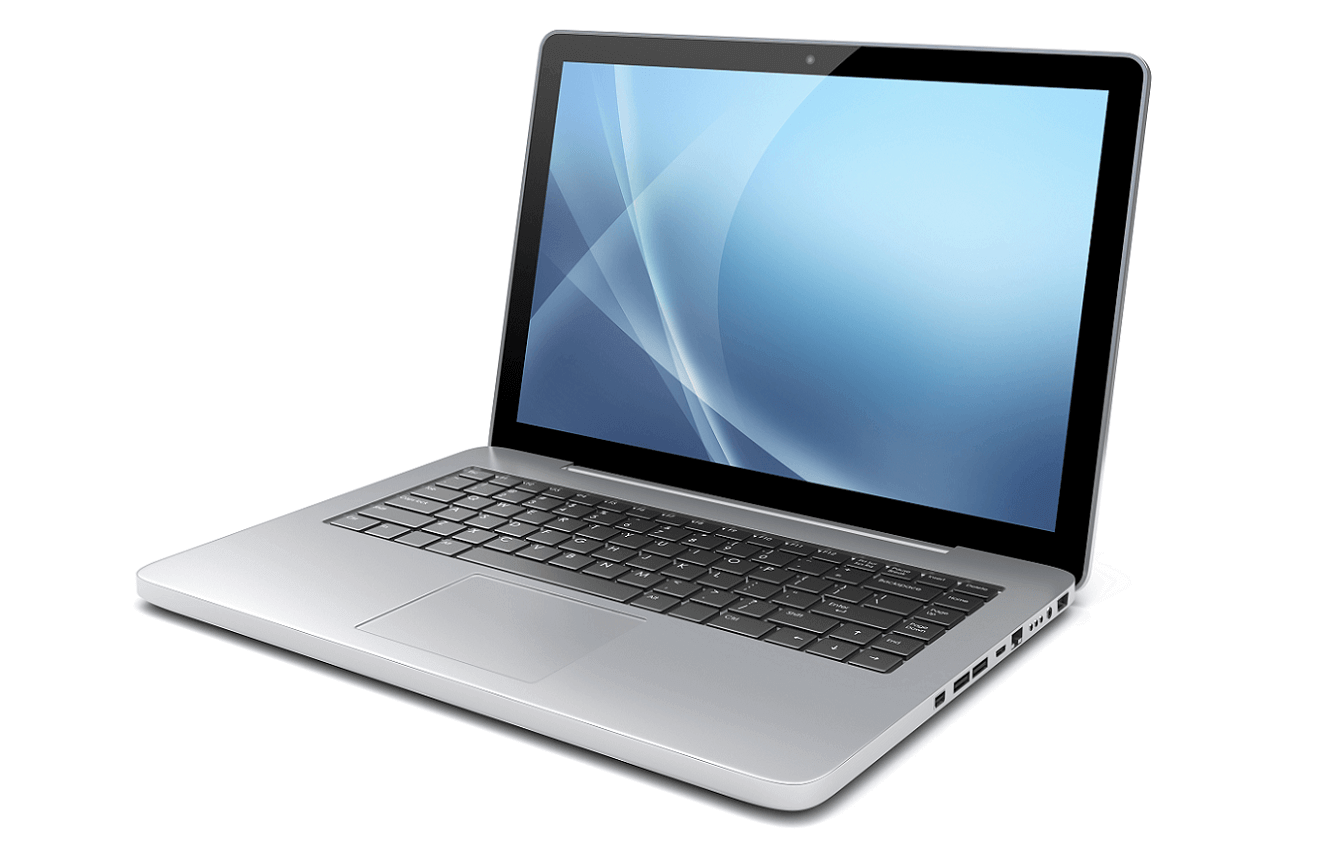
実は当社には、薄膜づくりに大変有利な条件がありました。それは、製膜法です。
TACフィルムには大きく2つの製膜法があります。原料となるTACを溶かすのに、溶剤を使うか熱を使うかです。さらに、溶剤を使う方法(溶液流延)では、液体をフィルム状にする際の基材の違いで、ベルト式とドラム式に分かれており、我々は写真フィルムの時代から溶液流延のベルト式を採用してきました。写真フィルムの時代はドラム式より生産性で劣っていましたが、薄膜づくりではこれが一転して有利であることが分かったのです。厚さが40ミクロンしかない光学フィルムを作れるのは世界で唯一、溶液流延のベルト式で技術を磨いていた当社だけだったのです。我々はその後も薄膜化では常にトップを走り続け、現在はモバイル用として20ミクロン(0.02mm)の製品も出荷しています。
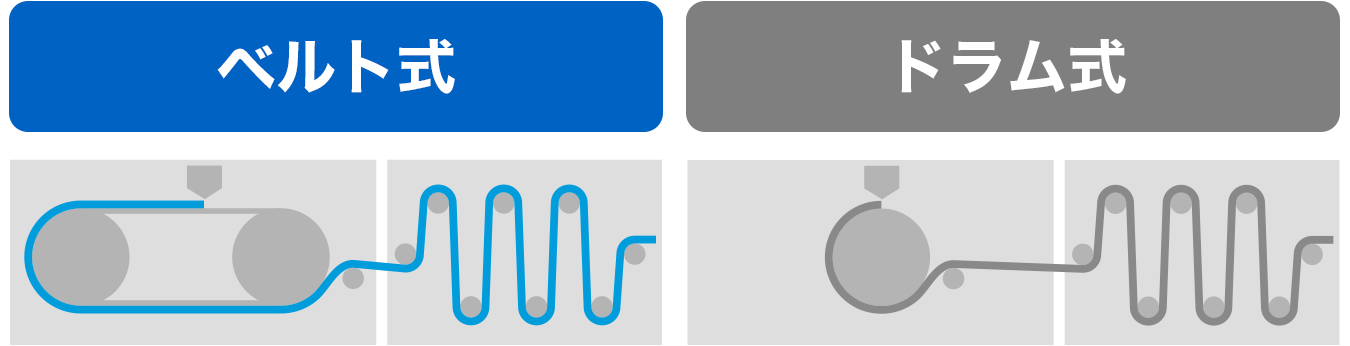
この実現の瞬間からTACフィルムの生産は、全くの異次元の難度の技術者集団、ビジネス集団に生まれ変わりました。
薄膜の開発によって新しい販路が広がりましたが、まだ安定して利益を確保できるほどではありませんでした。一方で、売り上げ増を見込んで、神戸事業場の既存ラインの隣に早くも第二ラインを新設し、2002年に稼働させる予定で工事が進んでいたのです。このままでは投資に見合う利益が出せず、事業が終わってしまうかもしれない――。
挑戦者がいてこそ時代は開かれる
もっと利益を出せる高付加価値な製品が作れないか? そこで目を付けた2つ目のテーマが、競合がすでに市場を独占していた視野角拡大用フィルムでした。これはTACフィルムに位相差という光学機能を追加することで、液晶ディスプレイを斜めから見ても真正面からと変わりなく明るくキレイに見えるようにする、つまり視野角を広げてくれるものです。ただし後発としての開発は難易度が高く、なかなか参入の糸口を見いだせないままに2年が過ぎようとしていました。
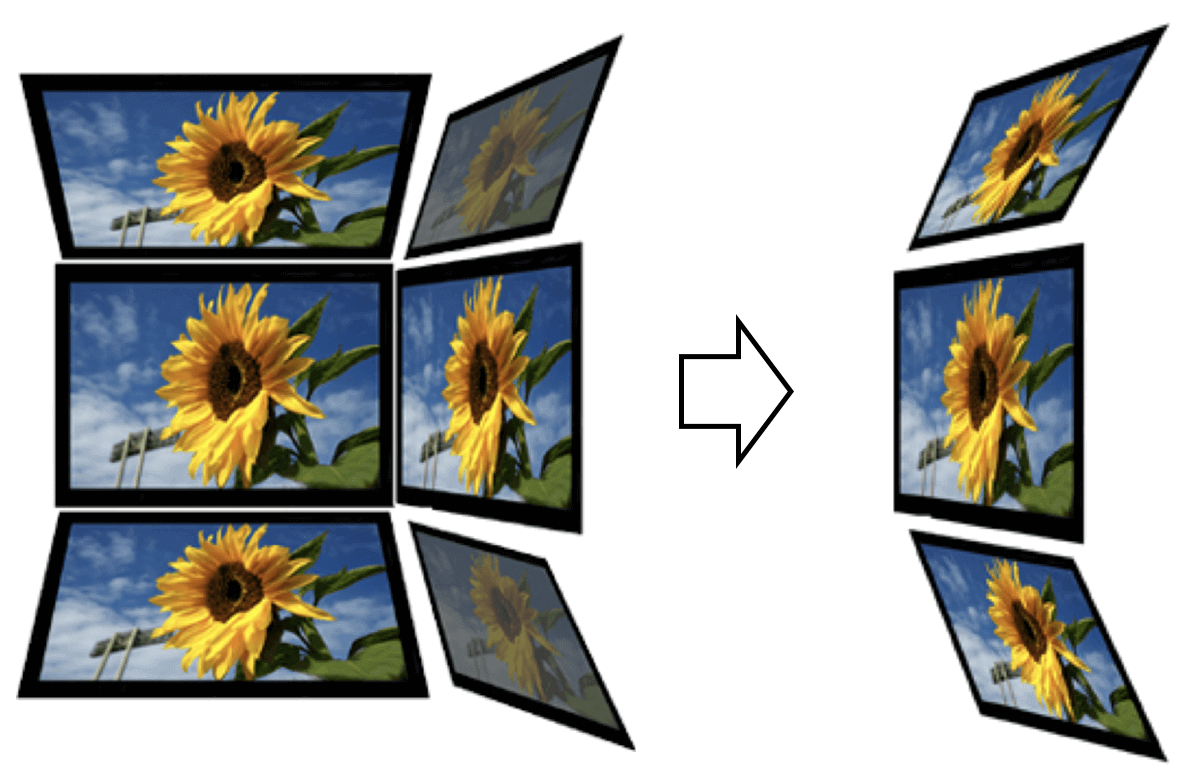
そんな中、2つの機会に遭遇します。1つは、社内で日の目を見ない別のテーマに関わる人やその技術との出会いにより、組み合わせと工夫が技術を価値に変える瞬間。もう1つは、フィルムを直接購入いただけるお客様に限定せず、サプライチェーンのその先の会社にも活路を求めて飛び込んだことによる、新しいお客様との出会いでした。
ある日、営業・開発一体でお客様訪問をしていた時に、次のような話を伺いました。それは、当時主流の駆動方式とは異なるVA(Vertical Alignment)方式が、映像品質に優れているとして液晶テレビ用に期待されていること、また、その視野角拡大には煩雑なフィルムの積層貼り合わせを必要とすることが、量産性の大きな課題であること、というものでした。社内で開発メンバーが苦戦していた視野角拡大用フィルムは、このVA方式であれば、社内で埋もれているあるテーマの技術と組み合わせ、さらに新しい発想を形にすれば、お客様にとってシンプルな工程で扱えるフィルムとして、自社で速やかに開発できるはず。ここで二つの糸がつながりました。そこで急遽、建設中のTAC用の第二ラインに必要な新工程を組み込み、VA方式に照準を絞って、視野角拡大フィルムの生産対応工場に作り変えました。
こうして2003年に誕生したのが、視野角拡大用フィルムと偏光板保護フィルムを一体化した「視野角拡大用VA-TACフィルム」です。最初に導入いただいたのは、台湾の液晶パネルメーカーでした。その会社を介して、同じく台湾の新興偏光板メーカーとの間で取引がまとまります。液晶では日本が圧倒的にトップの時代でしたから、彼らは挑戦者の立場です。いくら良い製品を出しても、試してくれる挑戦者がいなければ、世に出ることはありません。注目されていたVA方式はその後、液晶テレビで主力になり、導入いただいた会社も急成長を遂げました。むろん、我々の市場も一気に拡大したのです。
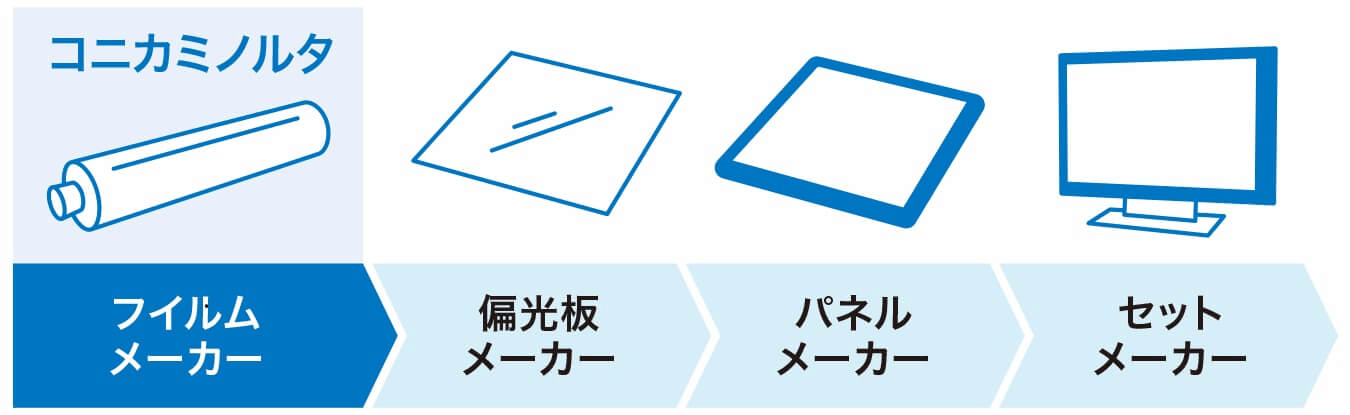
TACフィルム事業はそこで初めて、安定した収益を確保できるようになりました。この視野角拡大用フィルムと偏光板保護フィルムの一体化は、高価で複雑なフィルムの貼り合わせを必要とするが故の高価格化や大画面化への障害を取り除き、その後の大画面液晶テレビの普及に大きく貢献できたと自負しています。
お客様との対話をヒントに、
時代に見合う価値を
しかし、競合企業もさまざまな形で仕掛けてきます。そこでVA-TAC第二世代の開発では、厚さを80ミクロンからノートパソコン用保護フィルムと同等の40ミクロンに薄膜化して、高性能・低コストを追求しました。ところが大型の液晶テレビ用ともなると、大きいうえに薄いため、腰がなくへなへなです。偏光板メーカー、セットメーカーの方々からは「薄すぎて偏光板用途のパネルガラスにキレイに貼るのは難しいだろう」と言われてしまいました。そこで、偏光板を貼る装置のメーカーの扉をたたき、実証試験を繰り返して、きちんと貼れるノウハウを構築し、改めてセットメーカーに提案しました。お客様の信頼に応えることができたのは、開発・生産・営業が一体となり、お客様にとっての「新しい価値創造」実現を目指した諦めない精神の賜物でした。
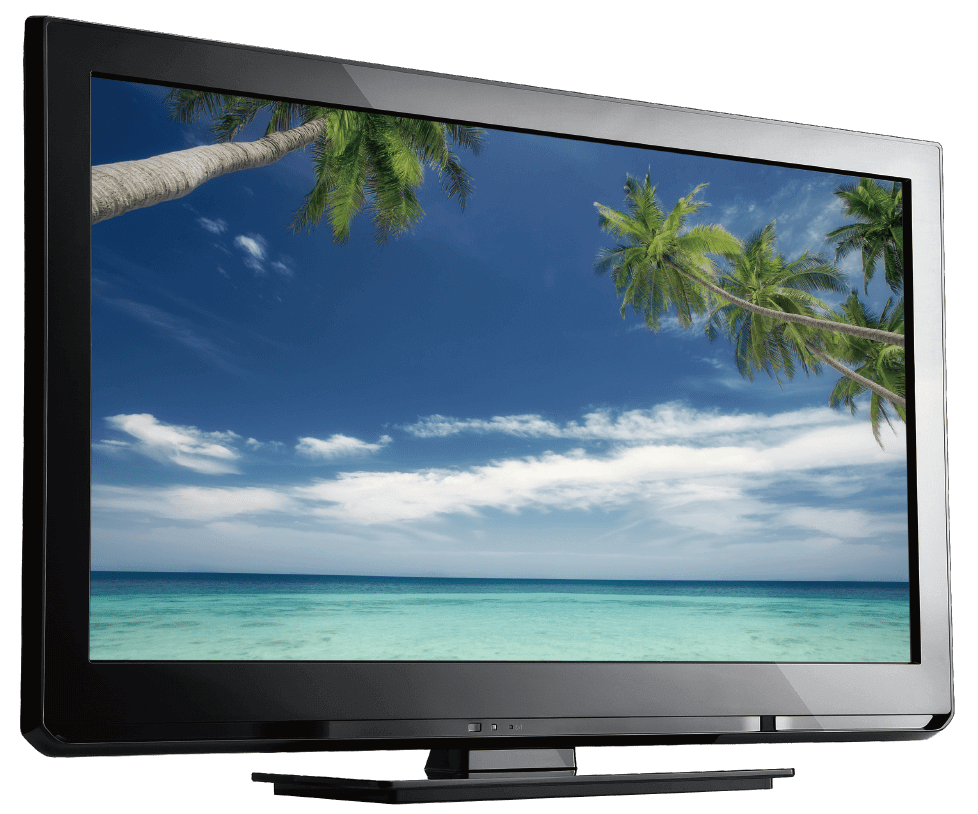
2005年頃の数年間は、急成長するディスプレイ市場を背景に、毎年の難しい果敢な投資判断の連続でした。自社完結する写真フィルムとは異なり、電機業界のお客様のスピードで化学プラントをマネージし需要を見通すだけでなく、お客様との確固たる関係を構築して2~3年後の需要に応えていく必要があります。その投資額も当時の事業の年間売上の半分を超える額が必要でした。
時代が進み2010年代半ば以降になると、お客様の生産プロセスが変化し、加工工程が一つの工場の中で完結せず、むき出しのパネルの状態で海上輸送されるケースが出てきました。その際に、フィルムが湿気を吸って光学特性が変化するというTACの弱点が問題となったのです。水に馴染むのはTAC系材料の特性そのもので、耐水特性を持たせることは原理的に不可能、という周りの声に屈することなく、化学の知識をフル活用して、やっと親水性でも光学的に効果的な添加剤を見つけその問題をクリア。今ではその製品が主力となっていますが、ここでの悪戦苦闘がなければ事業が終わっていた可能性さえありました。このような開発の端境期には、特にお客様との関係を磨き続ける営業の頼もしい底力が発揮されました。
そんな危機にあたり、さらに先を見据えて同時にトライしていたのが、耐水性に優れた新素材、シクロオレフィンポリマー(COP)です。当社の生産技術と新しいプロセスやアイデアを組み合わせることで、TACや既存のCOPでは実現困難な、幅広で長尺なロール状にすることができる新しいCOPは、偏光板メーカーの工程を効率化できるのではないかと期待されています。
また最近は、フィルムの性能や品質というような技術的な側面から、生産の工程でどれだけ環境への負荷を抑えられるか、というような社会課題への対応に軸足を移しつつあります。そのような中で、広幅化や長尺ロール等によるお客様の生産工程改革や、新世代のバイオマス由来のTACといった、これからの課題にも向き合う準備も進めています。
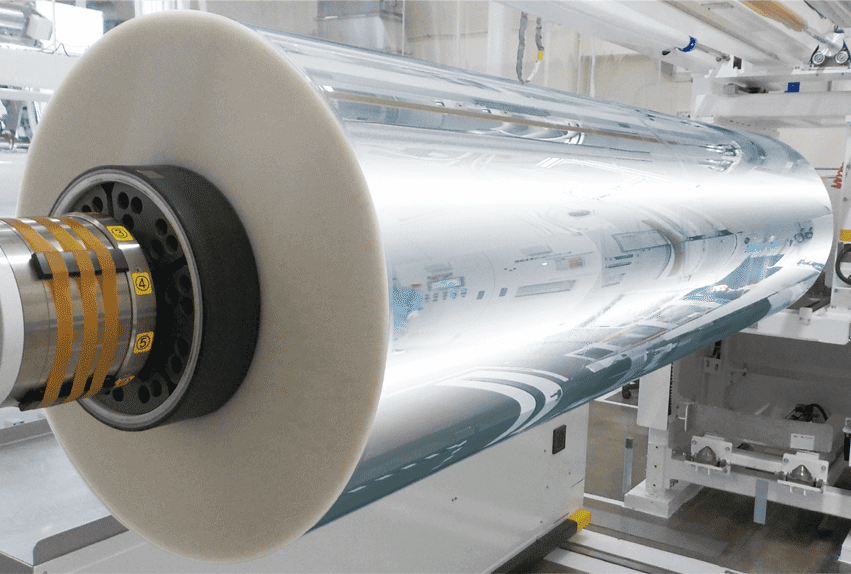
ビジネスの基本は、お客様が実現したいことを汲み取る対話から始まり、お客様も気付いていない設計や商品開発に繋げていくことです。競合にとっては苦手なところ、しかしお客様にとっては価値のあるところを、意識的に打ち出していく――。幾たびにも渡る危機においては、常にその姿勢を貫いてきました。
我々の強みは、個々の特別な技術ではなく、総合力です。ハンディキャップでさえも、どう克服しようかと知恵を出して、逆転の発想で切り抜けてきました。その時々に挑戦者であるお客様に助けられてきたように、我々自身も挑戦し続けなければならない。それこそが成長の源であると信じています。
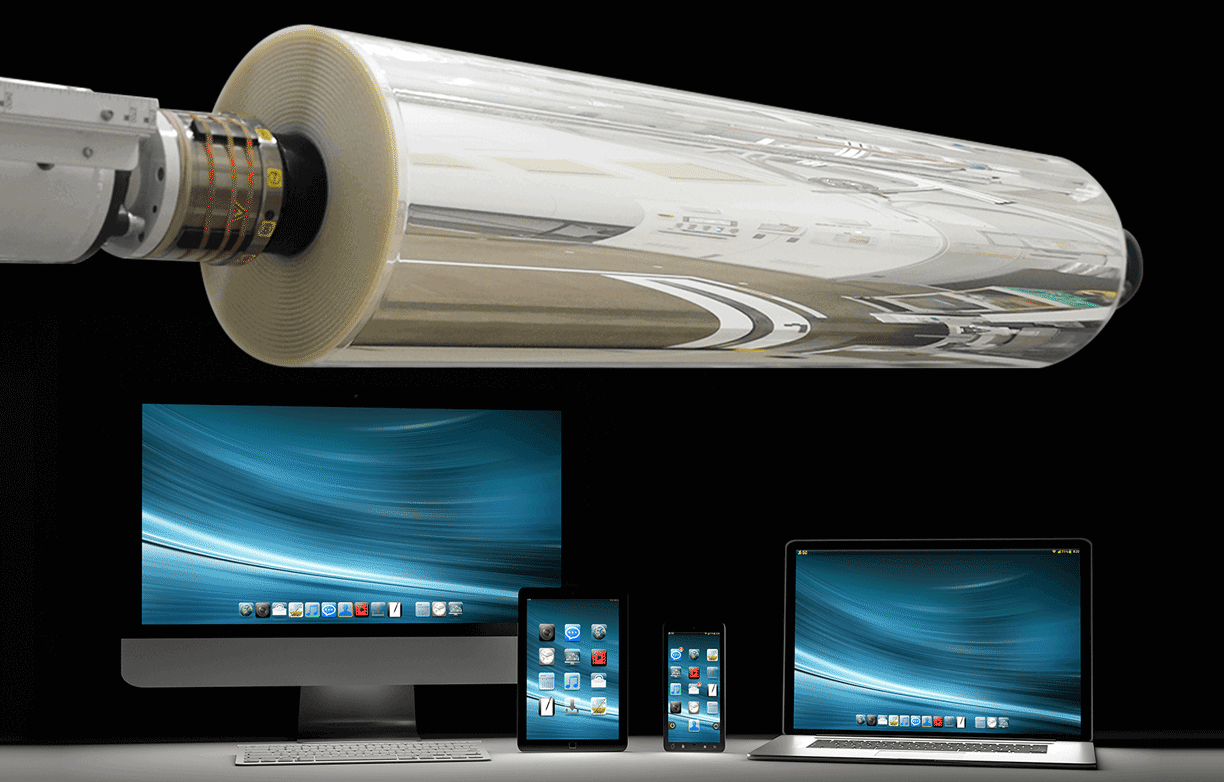
2003年に経営統合する以前の2社はそれぞれ社名変更を重ねてきたため、経営統合直前の両社のブランドであるコニカ、ミノルタという呼称で統一しました。
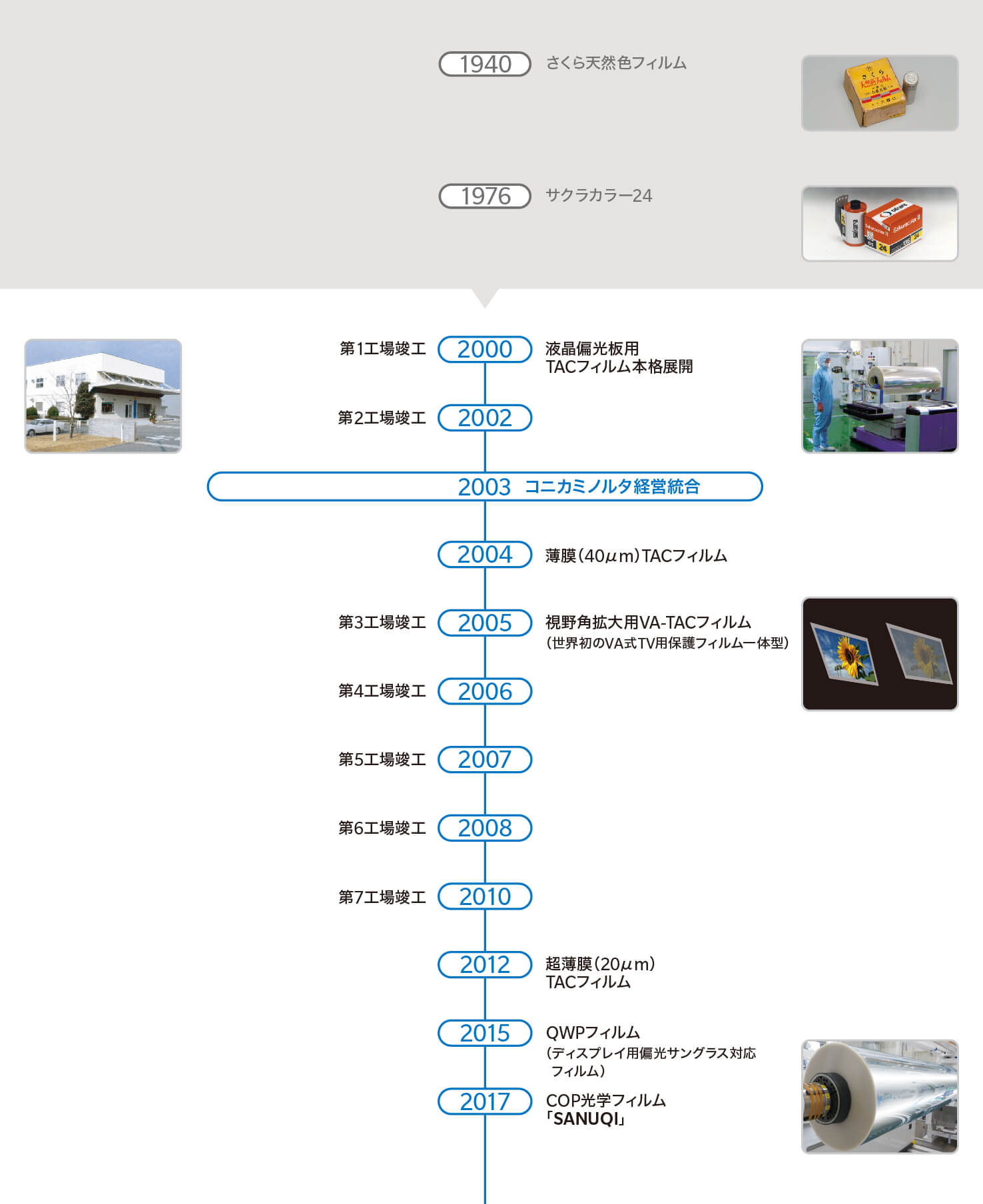