イノベーションストーリーズ
プロダクションプリント
プロダクションプリントの源流をたどる
印刷業界のアタリマエを変えた
画期的な提案の歴史
- 目次
印刷は写真と並び、コニカミノルタの創業時から続く事業の一つです、というと驚かれるかもしれません。実は150年前の創業当初から、印刷が日本で発展する原点となった、石版印刷(リトグラフ)用の材料や機器の輸入・販売を行っていたのです。その後、自社製の写真フィルムやX線フィルムの事業を拡大しながらも、印刷現場とは繋がりを保ち続け、1970年代にはオフセット印刷(アナログ印刷)に用いる製版用フィルムの開発・生産を開始し、印刷現場に届けてきました。当社と印刷業界との間には、長く、深い繋がりがあるのです。
こうした深い繋がりを礎に、印刷業界向けに製品・サービスだけでなく、技術サポート、コンサルティングを提供しているのが、現在のプロダクションプリント事業です。印刷の方法がアナログからデジタルに徐々に移り変わっていくことが見込まれる中、デジタル印刷を核とするプロダクションプリントは当社の成長領域の1つとなっています。
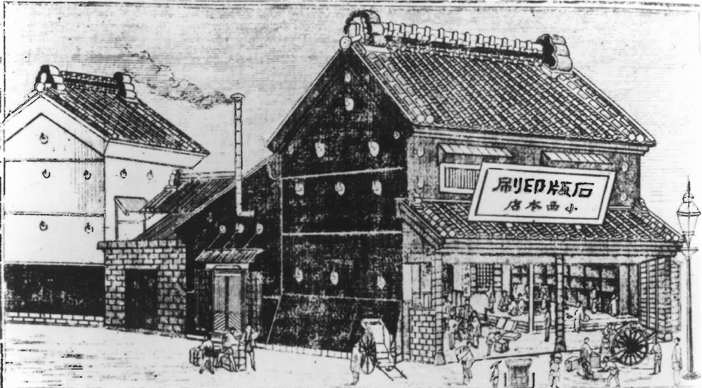
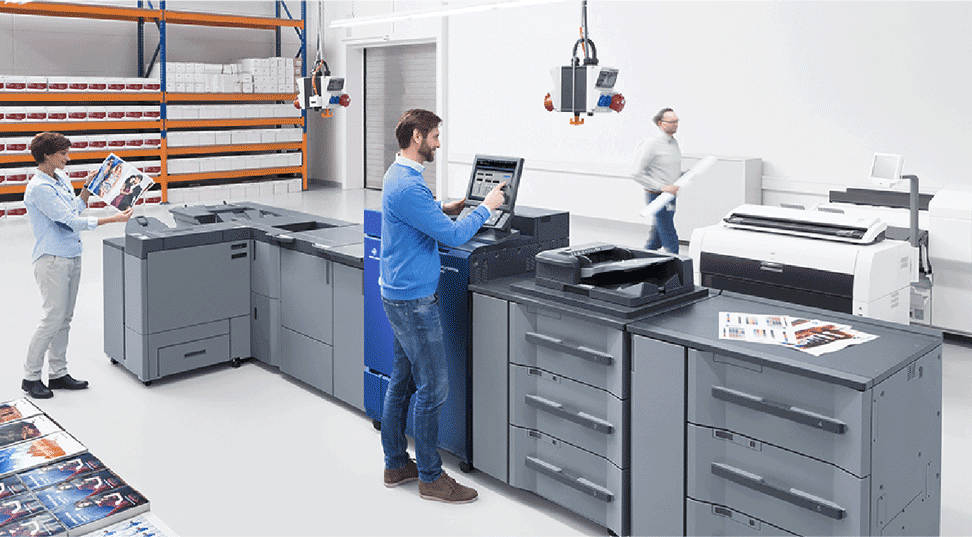
色校正が「コンセ」と呼ばれた理由が
ここにある
事業の歴史を語るうえで欠かせない製品が、1987年にコニカが発表した簡易色校正システム「Konsensus(コンセンサス)」です。
色校正とは、実際の印刷に先立って試し刷りを行い、指定通りの色に仕上がっているか、事前にチェックする工程です。当時、色校正は、実際の印刷版を用い、本番用の印刷機や色校正専用の印刷機(平台校正機)で行っていました。ところが、それには時間と手間がかかります。本印刷と同じ色再現を実現することが難しく、熟練工の技術を要しますし、部数も1部や2部だけ印刷する、というわけにもいきません。
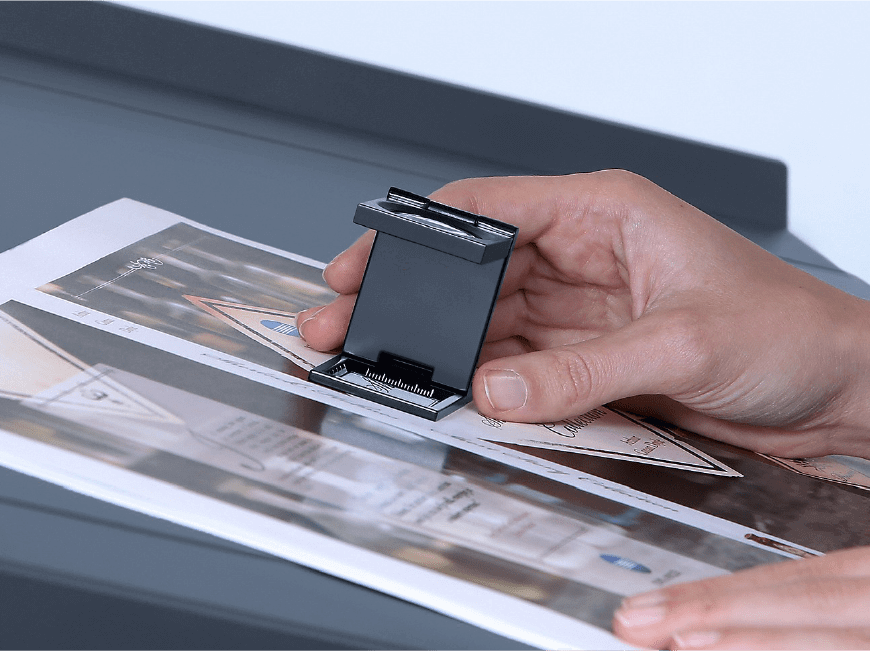
「色校正紙を、もっと簡単に出力できないものか?」技術上の課題の一つは、画像の濃淡を決める網点(あみてん)を本印刷に近い形でしっかり再現することでした。再現が不十分だと、色校正では問題ないように見えても、いざ本機で印刷した時に網点が重なり合い、互いに干渉を起こして「モアレ」と呼ばれる縞模様が発生してしまうかもしれませんし、写真の細かいディティールの良し悪しを判断することができません。
「網点をしっかり再現できる技術はないのか?」。開発チームが着目したのは、社内の技術、昔から培ってきた銀塩カラー写真の技術でした。印刷に近い画質表現を実現するための技術的なハードルは相当に高かったのですが、スピーディーに色校正を出力できる画期的な簡易色校正システム「Konsensus」を完成させたのです。銀塩カラー写真技術をベースに、柔軟でオリジナリティ溢れる発想で、より印刷物の画質に迫る改良を次々に重ね、ランニングコストも大幅に抑えました。
この簡易色校正システムは世界中で高く評価され、印刷業界に瞬く間に広まりました。なかでも日本では、印刷業界だけでなく、そのお客様である出版業界でも、色校正を「コンセする」と呼ぶほど、校正刷りのスタンダードになったのです。
当時は、デジタル印刷幕開けの時代。その後、印刷製版用フィルム事業の伸びに陰りが出始めた時代に、Konsensusは印刷製版フィルムを使うアナログKonsensusから、印刷データから直接レーザー露光するデジタルKonsensusへと進化を続け、印刷業界との間に絆を繋ぎ続ける存在となりました。
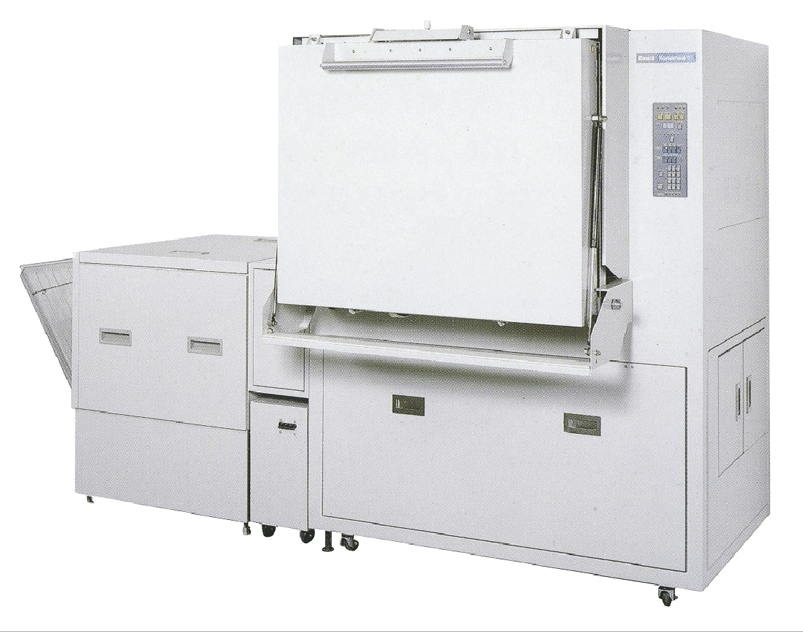
「これなら使える!」という
現場からの声
歴史を語るうえで欠かせない製品が、もう一つあります。印刷業界との絆の強さと、1990年代に磨き上げてきたカラー複写機の技術、この2つをもとに、2003年に生まれた「高速デジタルカラー複合機8050」です。デジタル印刷への移行に真正面から向き合うことを決めた後の、最初の大ヒット製品でした。今までデジタル印刷を敬遠していた印刷現場からも「これなら使える!」という声が聞こえてきた製品でした。
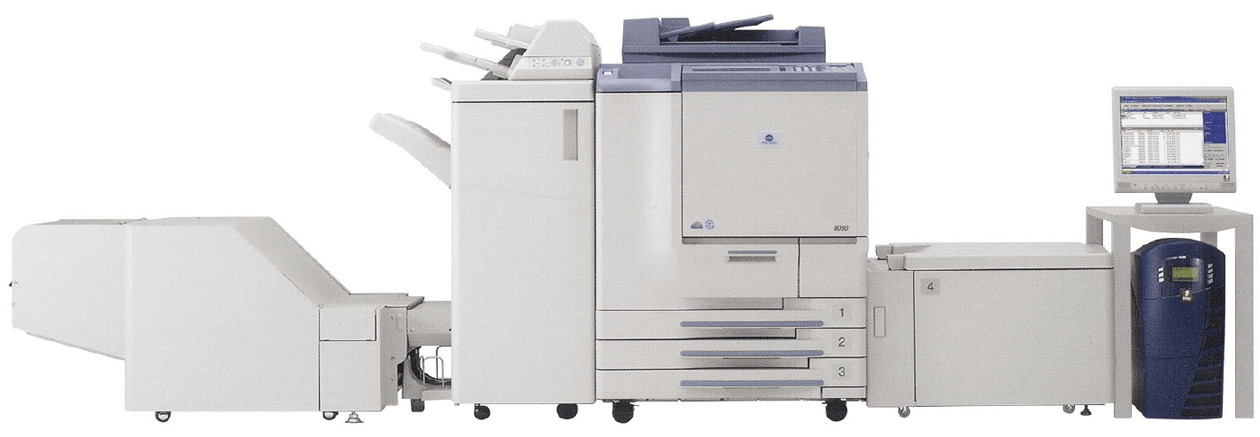
印刷業界をよく知る営業担当者が開発目標を出し、複写機エンジニアがこれに応えるかたちで開発は進められました。特にこだわったのは、印刷の速さ、品質の高さ、使える用紙の種類の幅広さ、という3つの点です。アナログでできてることをいかにしてデジタルでできるようにするか、ということを追求してきたのです。また、お客様にとっては価格も重要です。高い性能を目標に掲げながらも、価格をできる限り抑えることも要求されました。
「そんな無茶な注文を......」。時には、開発にあたるエンジニアが戸惑ってしまうような難問が寄せられることもありました。表面にコート剤を塗ったコート紙も印刷用紙として使えるようにしたいという注文がその一つです。
当時主流だった粉砕法トナーは、用紙上に定着させるのに190°Cもの高熱を加えます。コート紙にこのような高熱をかけると、蒸発する水分が表面のコート剤に妨げられて気泡ができてしまうのです。
突破口を開いたのが、1990頃から開発を進めていた重合法トナーです。大きな塊を作り粉砕して作るトナーと違って化学的に組成されるため、粒形が細かく均一で、印刷物の画質を格段に高めるものです。さらに、粉砕法トナーよりも低い温度で溶けるので高熱をかける必要がありません。まさに、重合法トナーによって、デジタル印刷の次の扉は開かれたのです。
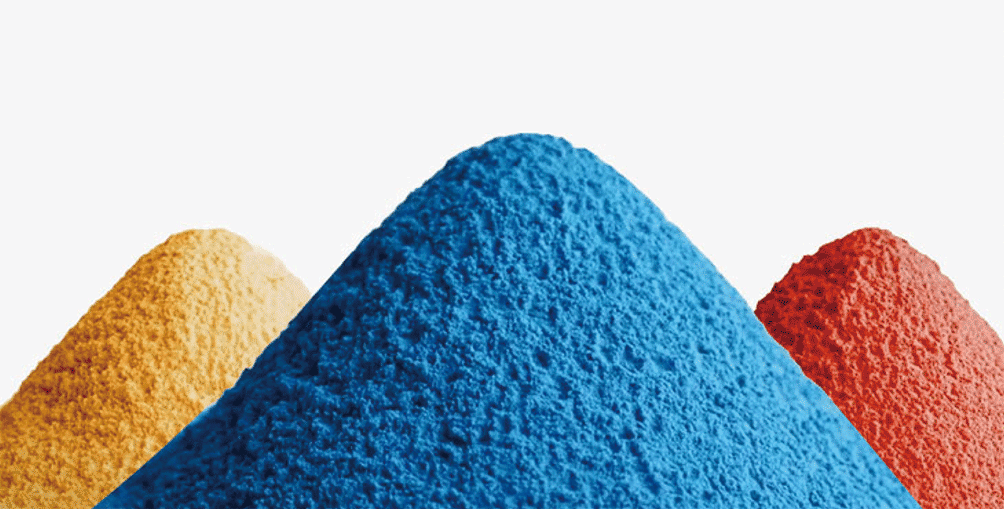
8050の大ヒットの鍵は、性能と価格のバランスをとことん追求した結果、デジタル印刷の導入機として定評を得ることができた点です。デジタル印刷の導入については、業界大手でさえ試行錯誤を重ねていた時代でした。規模の小さな印刷会社になると、印刷機が高くてとても手を出せない。そこに、我々が風穴を開けたのです。8050の出現で、デジタル印刷の市場自体が一気に倍以上に膨らみました。
なぜ、印刷現場のワークフロー改善を
目指したのか
コニカミノルタは2007年、印刷フィルムの事業をやめ、全リソースをデジタル印刷に集中していきます。しかしそれからも、印刷業界との絆の深さに変わるところはなく、その強みはますます生かされていきます。
その象徴が、2017年に発表した自動品質最適化ユニット「インテリジェントクオリティオプティマイザー IQ-501」です。
このユニットは、印刷現場で人手と熟練者の技術が求められる濃度・色調管理や表裏印字の位置調整などを、独自の技術で自動化するものです。開発に当たって考えたのは、「印刷会社のワークフローを改善し、処理能力を上げていくにはどうすればよいのか」ということです。これは、価格性能比を上げることに重点を置いてきた従来の製品開発とは、がらりと発想が異なります。我々の製品・システム開発上の大きな転換点になりました。
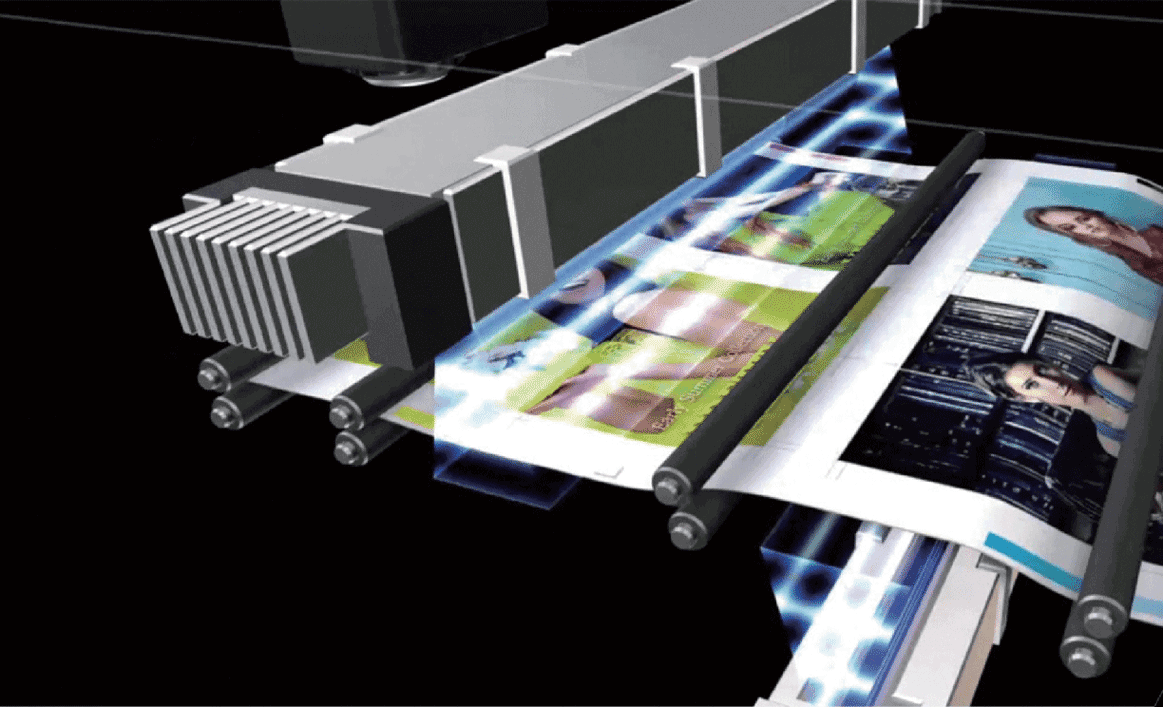
デジタル印刷機メーカーの多くがまだ、印刷機自体の性能の向上に重点を置いて製品開発を進めていた時代、我々はなぜ、いち早く発想を切り替えられたのか。
話は、その5年ほど前にさかのぼります。当時、デジタル印刷システムの普及速度が思ったよりも鈍化していました。「どうしてなんだろう?」―― 。そこで行き着いたのは、印刷会社にとってデジタル印刷は収益をもたらすものとは言い難い、という結論でした。
印刷現場では、受注から出荷までに掛かる「人手を介する作業」は平均65段階もあります。それなのに、発注者に費用を請求できる工程は、印刷や製本だけ。全体の1~2割程度です。さらに、作業のやり直しや操作ミスによる廃棄など、費用を請求できない作業や手間が非常に多い。それでも、受注規模の大きなアナログ印刷なら売り上げ全体の中でコストを吸収できました。ところが、小ロットで1オーダー当たりの売上が小さいデジタル印刷では、そうはいかないのです。
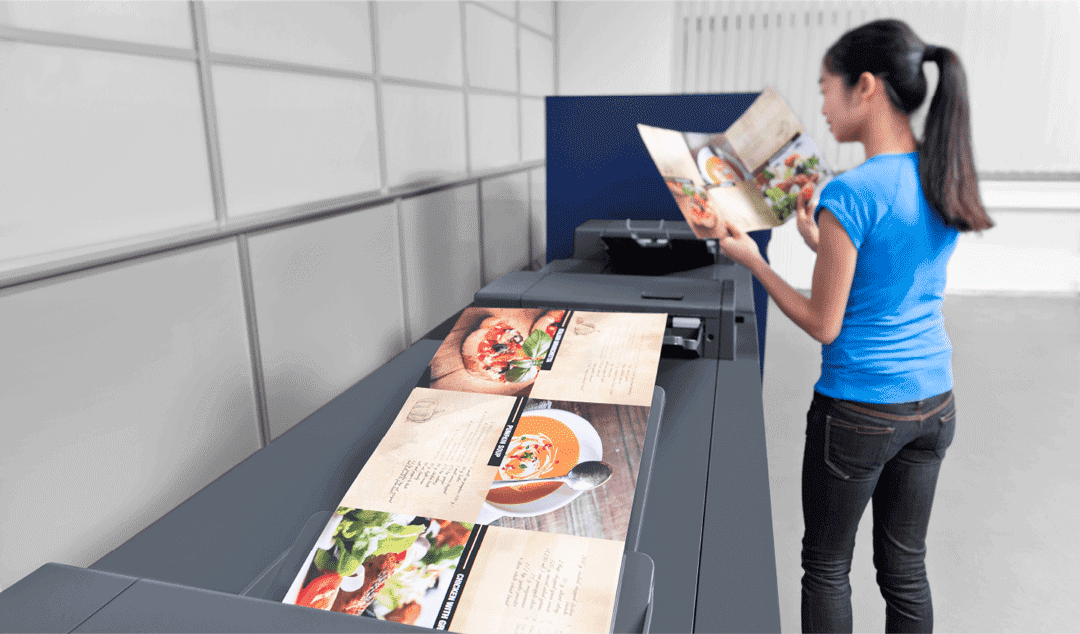
「印刷以外にかかっている作業を減らそう!」。そうしてデジタル印刷で収益を上げられるようになってもらう。オペレーターが時間をかけてこなしていた印刷の前工程、後工程の作業を自動化したのは、そのためです。作業時間を短くすることで、印刷機のダウンタイムを減らそう、と考えたのです。印刷会社でも当たり前だと思っていたことに、当たり前と思わずに取り組めたのは、お客様の現場に深く入って、本当の困りごとを見いだせたからなのです。
色調管理の自動化には、技術的な裏付けもありました。光やモノの色を計測するセンシング技術です。その源流は、ミノルタ時代の優れた測光技術にあります。この技術は国際的にも高く評価され、1967年には米航空宇宙局(NASA)の要請を受け、宇宙空間で利用する露出計「ミノルタスペースメーター」を開発した経緯もあるほどです。ここでもまた社内の技術力のシナジーが発揮されたのでした。
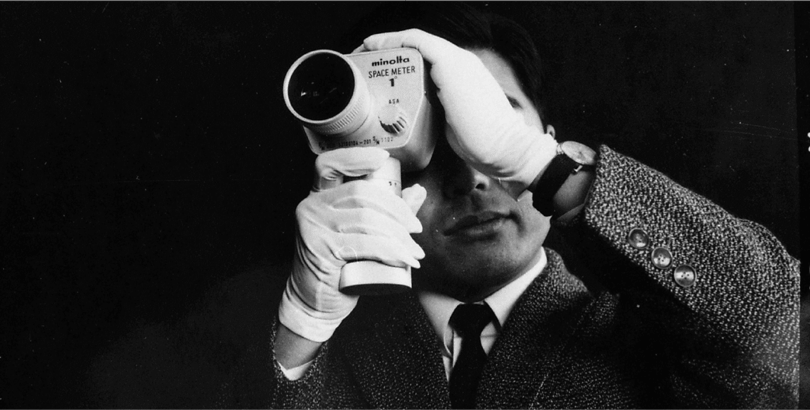
印刷現場のワークフローに目を向けた斬新な発想はお客様の賛同を得られ、IQ-501は今、印刷業界で確かな地位を築いています。
印刷業界では、熟練のオペレーターが減り続けています。人手や専門性が求められる作業の自動化を進め、印刷品質のばらつきをなくすことは、業界にとって対応が急がれる課題です。アナログからデジタルへの転換の機運が、今後もますます高まっていくなかで、プロダクションプリント事業が向き合うべきは、そうしたお客様の課題なのです。
現在、「気候変動への対応」や「有限な資源の有効利用」など環境面での対応が求められています。デジタル印刷には、必要な時に必要な量だけ印刷できるというメリットがあり、これは確実に環境負荷の削減につながります。また「版」を用いないため、アナログ印刷に比べ、資材を減らすことができます。こうした環境への貢献も、プロダクションプリント事業の果たすべき重要な役割として、今後もお客様とともに歩みを進めてまいります。
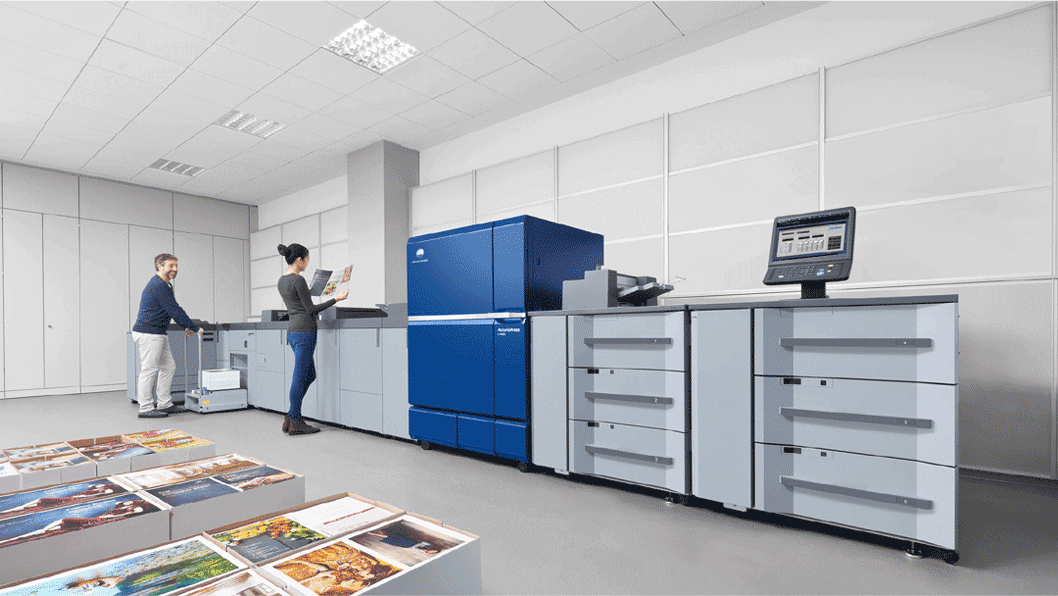
2003年に経営統合する以前の2社はそれぞれ社名変更を重ねてきたため、経営統合直前の両社のブランドであるコニカ、ミノルタという呼称で統一しました。
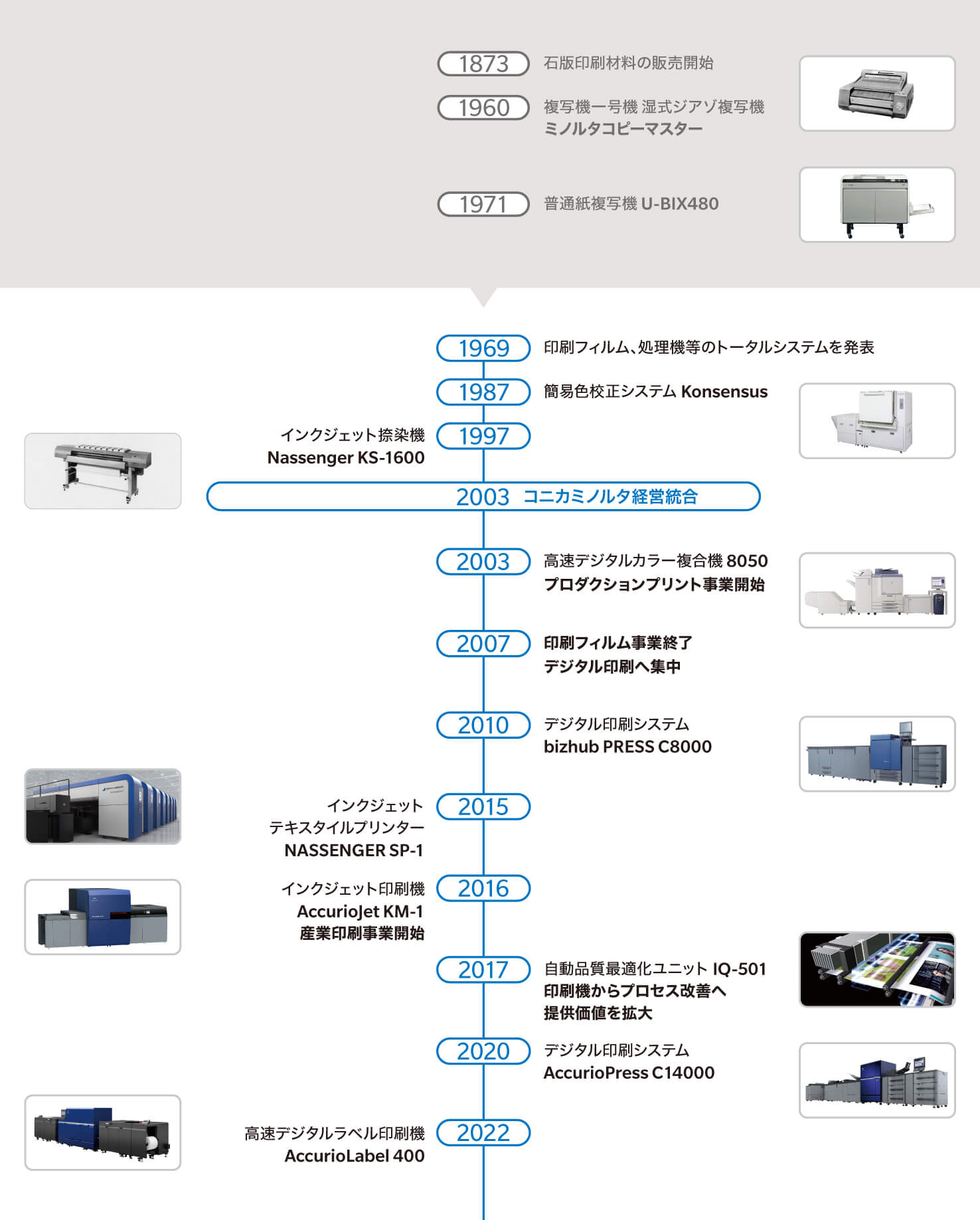